INVESTMENT CASTING

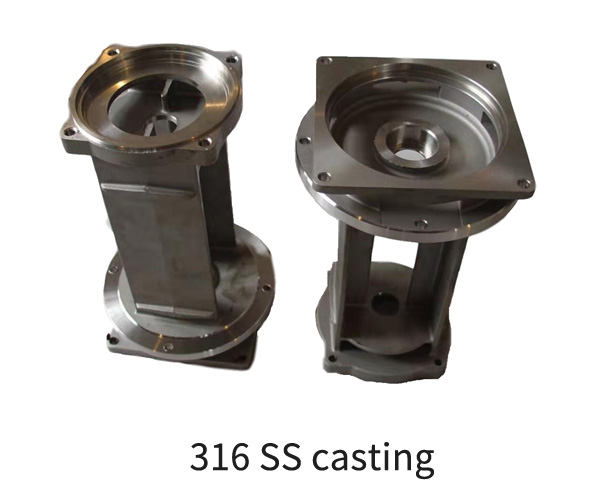
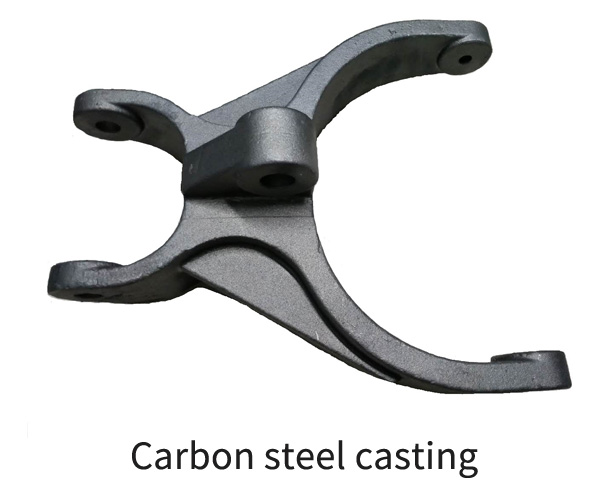
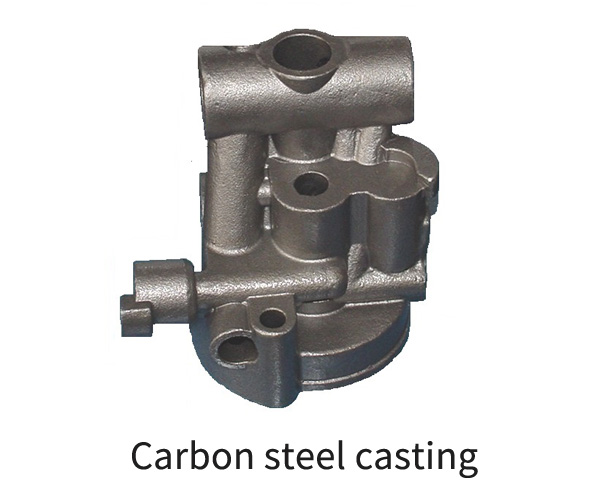
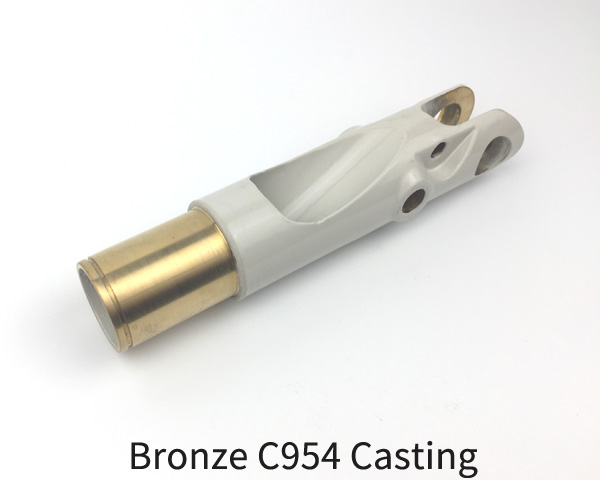
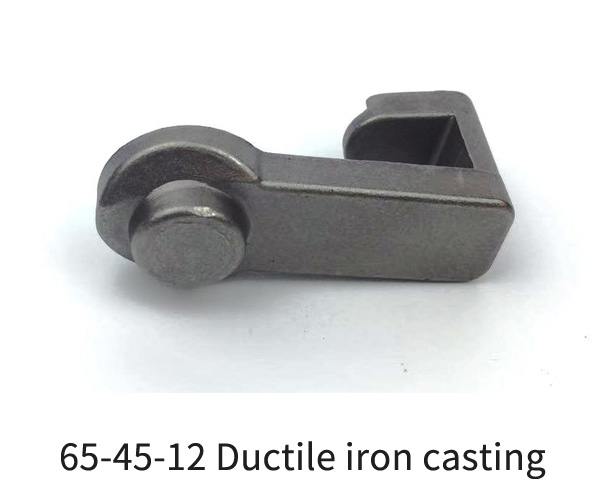
To strive for best price with high quality of castings for our customers is our goal from the starting of our business. Our system of quality control and inspection , Based on ISO9000:2000, is having played more and more role in product quality. It is our strong quality control that is ensuring us to supply thousand tons of investment casting to our customers every year. These castings involve quite wide material with standards: SAE, ASTM, DIN, BS, JIS, ISO etc. Some popular materials are for our customers in USA as follow:
● Carbon steel casting: 1020, WCA, WCB, WCC All types of carbon steel
● Low alloy Steel casting: 8620, 3140, 4340, etc all types of alloy steel.
● Stainless steel or nickel alloy casting,
304, 316, 310, 17-4PH, HH, HK etc High heat and wear resistant alloys
● Bronze casting: C952, 953, 954, 17200...
● Ductile iron casting: ASTM 65-45-12,
● Aluminum casting: ASTM 319, 356, 357,
Casting Weight: 0.011lb~110lbs (0.005kg~50kgs)
Almost net-shape dimension and good surface finish with our investment casting process will produce the most complex, finely detailed lost wax castings possible. Competitive price, qualified part and scheduled delivery will keep you ahead of the competition.
Every customer’s requirements are carefully scrutinized in contract review and confirmed so you are confident your investment castings are ideally suited to your needs before proceeding. It has to be right for you! If you could not know if your part is good for investment casting, we can provide you our best suggestion for your decision! H&E is looking forward to being your supplier for ONE stop of services.
H&E can take “Total Product Responsibility” by including machining; heat treating (including Carbonizing, etc.), coating, polishing (including electrolytic polishing) and plating
What we need is a print or a sample; you can get our free valuations for your parts.
We have two kinds of investment casting process. One is being used in the world
called Silica Gel process. Its advantage is better surface finish and tight tolerances of dimension. But an disadvantage is higher cost than another investment casting process called sodium silicate process. The later can make castings with not too better surface finish castings than the former process. but It has lower cost than the former. Usually, the later is being used for production of carbon steel, low alloy carbon steel, bronze, ductile iron to lower cost. But Silica gel process also can be used for these castings and also stainless steel castings.